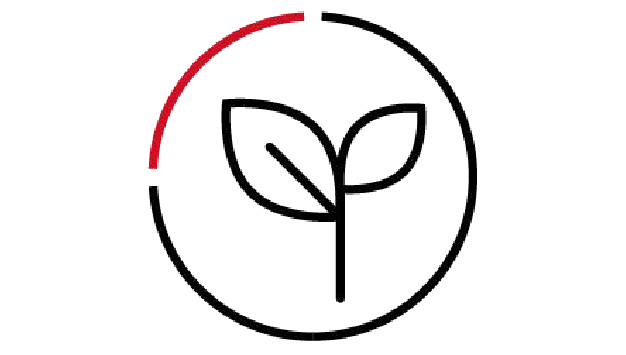
How RTX is engineering sustainable flight
Across the company, engineers are working to help aviation reach its goal of net-zero carbon emissions by 2050
On a Thursday afternoon, after a day of prepping and months of planning, a team of engineers watched and listened as an intricate weave of wires and metal on a tabletop buzzed and hummed.
The machine they’d built didn’t look like much, but it was, in fact, a prototype for a new turbogenerator, the part of an engine that turns energy into electric power. And its successful 15-minute run test was a major milestone for the STEP-Tech demonstrator, a project to give small aircraft the capability of hybrid electric flight.
STEP-Tech, a collaboration of teams from across RTX, is part of a growing body of work at the company to make aviation more sustainable.
“It’s every engineer’s dream to work on something new and cutting-edge,” said Zubair Baig, who leads the development of STEP-Tech and oversees electric propulsion for Pratt & Whitney, an RTX business. “The amount of work to be done between now and launching a product is astronomical, and I think, for me, that’s exciting.”
That sense of excitement and ambition extends throughout RTX, where experts are working in support of the aviation industry’s goal to reach net-zero carbon emissions by 2050. That work includes:
Achieving the goal will require a combination of approaches, said Juan de Bedout, RTX's vice president of aerospace technology.
“Since the dawn of aviation, our industry has been working to improve efficiency every year,” said de Bedout, “and now the challenge is to drive that pace even more aggressively.”
Here are some of the questions RTX is answering to make sustainable aviation possible.
What if aircraft engines were electric?
The engines Pratt & Whitney produces already are 70 percent more efficient than they were 30 years ago, said Graham Webb, the business’ chief sustainability officer. In 2022 alone, more than 1,000 orders for the company’s GTF engines will reduce fuel consumption and carbon emissions by 16 to 20 percent compared to the previous generation.
But new hybrid electric technology, he said, would reduce emissions even faster.
“I look at it as enabling the next 100 years of Pratt & Whitney,” Webb said.
In Quebec, Canada, RTX is working with the federal and provincial governments on a regional aircraft flight demonstrator that would use a one-megawatt electric motor from Collins Aerospace to help power the takeoff and ascent – the most energy-intensive stages of flight – of a De Havilland Canada Dash 8-100 turboprop plane. In December 2022, a hot engine test showed the concept is on track for flight testing in 2024.
The system is expected to reduce fuel burn and carbon emissions on small aircraft by 30 percent, and could also bring a significant reduction when scaled up to larger single-aisle passenger planes.
“I think it just shows the power of what we can do,” said LeAnn Ridgeway, chief sustainability officer at Collins Aerospace, an RTX business. “Once you start designing together, you’re getting all kinds of efficiencies, and that’s pretty exciting.”
There’s a similar level of collaboration in STEP-Tech, which stands for scalable turboelectric powertrain technology. The project, based at the Raytheon Technologies Research Center in Connecticut, consists of a “Lego set” of modular components that will allow the team to test various configurations quickly.
It has three sections, set up in the lab similar to how an aircraft would produce power. On a jet burner stand, there’s a turbogenerator that connects to the electrical section, which consists of lithium-based batteries, supercapacitors and a high-voltage power distribution system. That section powers a series of fans that create propulsion in an acoustic wind tunnel.
The project’s creators can easily swap out any piece of the demonstrator to see how a slightly larger motor would perform, for instance, or use 3D printing to create plastic fans of different sizes and shapes.
“We’re leveraging modularity and scalability,” Baig said, “to be able to test and learn on different architectures very fast.”
The demonstrator is focused on concepts in the 100- to 500-kilowatt class, with potential to grow up to one megawatt, and it has applications in commercial, military, unmanned and passenger aircraft. With its first test complete, Baig and his team will use the data gathered to refine their concept and complete a full system test.
Seeing STEP-Tech successfully test its first prototype has been one of Webb’s favorite moments of the year.
“It’s always great to talk concepts and work with models and those types of things,” Webb said, “but when you actually have hardware to bring together, fire it up and it works – that, for an engineer, is what it’s all about.”
How can we use new fuel sources?
By using sustainable and alternative fuels, Raytheon Technologies estimates the aviation industry could reduce carbon emissions by 80 percent. Sustainable aviation fuels, often called SAF, come from waste agricultural products like grain, or they are produced with renewable energy.
Roughly 1 billion dry tons of biomass could be collected every year for SAF. Increasing SAF production and use, Webb said, would result in the fastest and most sustained emissions reduction.
“That is the biggest lever that we have in our industry today to reduce our emissions,” he said.
Pratt & Whitney’s GTF engines are fully compatible with unblended SAF, and the rest of the company’s current engines can run on a blend of 50% SAF and conventional jet fuel. Engineers are working to make all Pratt & Whitney engines and all Collins Aerospace propulsion system components fully compatible with unblended SAF.
Raytheon Technologies is also looking to multiply the benefits of individual approaches by using them together. In a project called SWITCH, for example, several companies and industry groups have partnered to develop a propulsion system that improves fuel efficiency and reduces emissions by up to 25 percent through the use of hybrid electric and water-enhanced turbofan technology.
The concept would use Pratt & Whitney’s GTF engine, and it would be compatible with SAF and potentially hydrogen. The hybrid electric GTF powertrain will rely on megawatt-class generators and a high-voltage power distribution system from Collins Aerospace, while the water-enhanced turbofan will inject recovered water vapor from the exhaust into the combustion chamber.
“What I love about this is the industry is working together in a cooperative mode to develop these types of technologies,” Ridgeway said. “I’m a firm believer that cooperation is going to be an accelerator for us and get us as an industry to the finish line quicker.”
Can we fly smarter?
Walking onto an airplane, you might not think twice about the door, but its engineers certainly did.
“Packed inside that door is a whole bunch of mechanisms and electronic components,” Ridgeway said. “There are life rafts, the air lock, all kinds of sensors and the window itself.”
Each of those parts adds weight, and weight increases the aircraft’s demand for fuel. To mitigate that demand, teams from across Collins Aerospace worked together to design and integrate what they call a “One Door” concept. The prototype door is roughly 20 percent lighter than current aircraft doors, thanks to an 80 percent reduction in the number of parts, and the use of advanced materials like thermoplastics to replace items like steel fasteners.
Technology can help reduce time spent in flight, too. Collins Aerospace is finding new ways to use artificial intelligence and machine learning to find the most efficient real-time routes for aircraft. With less time spent circling or on the runway, just one aircraft could save 12,000 gallons of fuel per year.
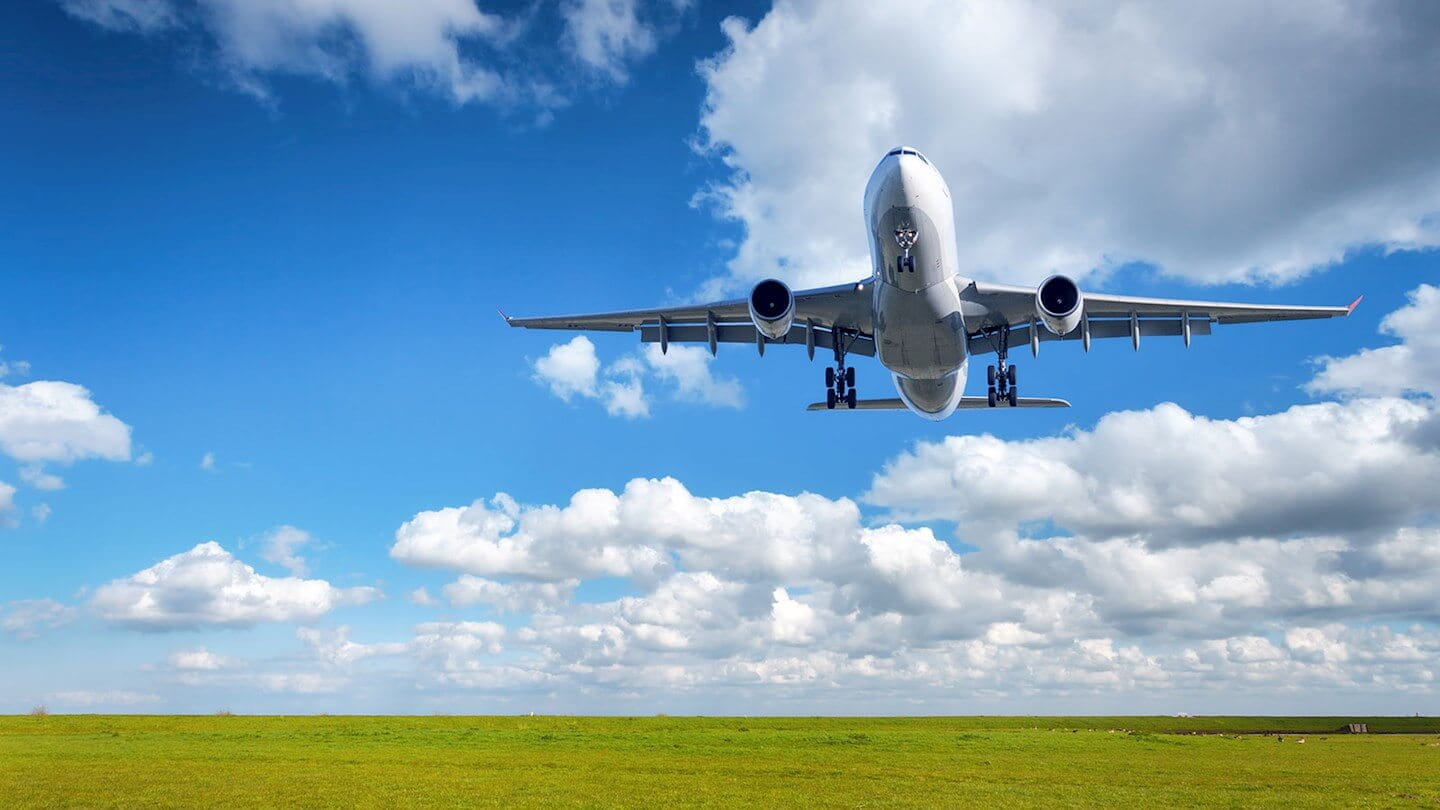
“Since the dawn of aviation, our industry has been working to improve efficiency every year, and now the challenge is to drive that pace even more aggressively.”
Juan de Bedout | Vice President | Aerospace Technologies
What will it take?
Raytheon Technologies’ sustainable-aviation efforts – electric propulsion, sustainable fuels, lighter aircraft and flight optimization – reflect many approaches but have one thing in common: They require the company’s corps of engineers and other experts to work toward a common purpose.
“It really is going to take all of these efforts coming together,” Ridgeway said, “in order for the industry to succeed at that net-zero goal.”